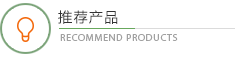
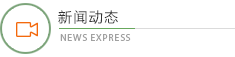

工业内窥镜搭载三维立体相位扫描测量技术在发动机孔探中的应用
一、从韦林工业内窥镜看工业视频内窥镜测量技术的发展历程
工业内窥镜的诞生是为了实现间接目视检查,而它应用于民航发动机孔探工作时,操作者除了需要通过它查找缺陷,还需要对缺陷尺寸进行测量,以便满足视情维护的要求。为了得到有判定价值的数据,最初采用接触式测量法,即在光学硬杆镜或柔性光纤镜探头上捆绑已知尺寸的参照物,通过它与被测物的直接接触人为地比较估算缺陷实际尺寸的大小。这种方法增加了探头的外径,并严重影响了探头的导向性能, 导致发动机内部需要检测的很多区域无法到达,且可能造成参照物因卡阻而脱落,形成发动机内部的多余物隐患。
随着美国韦林工业内窥镜在1984 年研制出全球第一台工业视频内窥镜产品以后,通过视频成像处理技术实现了非接触式的比较测量方法,很好地解决了上述问题。这种比较测量法是使用发动机内已知机构的尺寸作为参数,通过图像处理软件进行比较计算,从而得到测量数据。如将叶片气孔间距作为已知参考值,对该叶片上的缺陷尺寸进行分析测量。该方法要求已知尺寸与未知缺陷在同一平面上,且探头的镜头与该平面相对垂直,才能实现测量计算并具有起码的相对准确度。在遇有较大尺寸的缺陷且测量精度要求不高时,可以选用该测量技术。目前具有测量功能的工业视频内窥镜产品都有该测量方式。但对于民航发动机孔探工作需要检查的很多位置,操作者很难在相对垂直的同一平面上找到可作为比较计算参数的已知尺寸,并且这种测量的精确度仍不能完全满足要求。
美国韦林工业内窥镜在上世纪九十年代初所研发的单物镜阴影测量法技术首次实现了孔探工作中的精确测量,这种测量法是工业视频内窥镜上最早应用的非接触式精确测量技术(见图1),其在视频探头的测量镜头的照明光输出窗口刻有一道黑色直线, 当照明光通过时,会在被测物体上形成一条阴影线,探头距离物体的远近变化使阴影线在屏幕上的位置左右移动变化,而测量镜头上的单一物镜的成像视角不变,主机内的视频成像处理器会根据直角几何运算原理计算出测量镜头与被测平面的距离,从而进一步在该平面上计算获得测量点的二维坐标,以便进行各种测量模式下的精确测量(见图2)。这种测量法的缺点同样是要求测量镜头与被测面相对垂直(不垂直时,只能沿阴影线进行测量)才能保证测量精度,因而操作难度相对较高,应用上有一定的局限性。
为了解决这一问题,随后又出现了双物镜测量技术,用测量镜头上的两个物镜(见图3)之间的已知距离作为底边,通过与测量点所形成的顶角大小的变化,建立准确的三角几何计算关系计算确定测量点与镜头的距离, 并通过灰度识别区分不同的测量点, 进而计算获得测量点的坐标,以便进行各种模式下的精确测量(见图4)。由于采用夹角变化作为变量,不再需要镜头与被测物体垂直,一定程度上降低了孔探测量操作的难度和强度。但根据双物镜的设计原理,其镜头的视野相对单物镜减半,屏幕图像也被一分为二,不便于观察寻找及定位缺陷,所能测量的区域和缺陷大小也相对明显受限,并且测量点的位置及其匹配值(用来衡量选取的测量点识别合格与否的标准)正确与否,存在人为及系统误差的可能性。
无论是单物镜阴影测量法还是双物镜测量法,都是基于二维画面进行处理和计算的,并且变量参数(位移或夹角)少、三角几何计算的数学模型单一。为保证测量精度就要有较大的放大倍数,为此测量镜头的视野和焦距范围都偏小。需要首先使用视野范围相对较广、焦距范围相对较大的观察镜头寻找并发现缺陷之后,将探头取出更换成测量镜头,然后再次穿入发动机寻找缺陷进行测量。由于这两类测量镜头的视野很小(50°或60°)、焦距较近,很难快速有效地再次寻找到并达到缺陷位置,甚至有可能找不到缺陷;即便到达缺陷所在的叶片位置,也有可能因为角度或视野的问题,无法完整地捕捉到缺陷的图像。当面对超过测量范围(如双物镜测量在保证精度的前提下一次测量范围一般最大不超过15mm)的较大缺陷时,为了得到相对精确的数据,就必须分段测量,再将结果累加,严重影响了孔探测量效率和精度。近些年各型发动机的孔探穿绕工作呈逐步增多的趋势,发现缺陷后取出探头再次定位测量,在很大程度上影响了孔探效率,而且多次穿绕增加了探头的磨损消耗和发生卡阻的几率。这就要求工业视频内窥镜产品(孔探设备)具备缺陷的“即发现即测量”功能,同时尽量增大一次性测量的范围以及增加更多的测量模式,以便应对并满足越来越多、越来越复杂的孔探测量工作。
已于2005年隶属于通用电气(GE) 集团的美国韦林工业内窥镜于2010年年底推出的三维立体相位扫描测量技术可以很好的解决这一问题。该技术应用在其XLG3型工业视频内窥镜产品上,通过视频探头前端的三维相位扫描测量镜头上的两个可见光LED光栅矩阵(见图5),将频闪发射的多条平行阴影线交叉叠加投影到被测物体表面上,物体表面几何形状的变化会导致出现畸变的条纹(见图6),这些畸变条纹就包含了物体表面的三维信息。由视频内窥探头前端的CCD 摄像头摄取这些三维信息,主机内的计算机处理系统再对此进行扫描和运算处理, 然后根据相应的数学转换模型和重构算法对物体的轮廓进行三维重构,即获得了被测物体表面的三维坐标数据,进而就可以进行各种测量模式的具体操作,获得测量结果。
二、将搭载三维立体相位扫描测量技术的工业内窥镜应用于发动机孔探工作中的优点
三维立体相位扫描测量技术应用于发动机孔探工作有以下3方面优点。
1. 即观察即测量,孔探工作效率高
由于三维立体相位扫描测量技术不再是根据二维画面进行,而是采用摄取和扫描物体表面三维信息的办法,所以不再限制测量镜头的视野和焦距,可以采用单物镜且视野范围更广、焦距范围更大的设计,实现即观察即测量,发现缺陷后无需更换镜头即可直接测量(如图7所示)。近年来,虽然也有其他厂家尝试研发观察镜头与测量镜头二合一的技术以期实现即观察即测量的功能,但由于其测量精度无法满足要求而不被接受。
2. 视野范围广、焦距范围大
该3D镜头的视野为105°,属于广角镜头(见图8);焦距是8~250mm(前视)、7~250mm(侧视),焦距范围非常广,涵盖了普通观察镜头的极近焦、近焦和中焦的焦距段;适用范围广,观察到的画面整体更明亮,无论是检测发动机内各级叶片的狭小空间还是燃烧室等较大空腔(如图9所示)均能胜任。
3. 测量结果更精准
与单物镜阴影测量法和双物镜测量法均是先人为选择测量点再进行该点的坐标计算不同的是,三维立体相位扫描测量技术是通过系统的相位扫描与计算,首先构建出一个由无数的具有三维坐标信息的点云集合,然后由操作者选择测量模式并选取缺陷测量点,再由系统完成测量;对于无法获得三维坐标也即无法测量的区域直接使用红色体现,系统禁止在这些区域选取测量点;操作时不需要阴影线的鉴别、测量点的匹配等步骤。不仅具有极强的易用性,也意味着尽可能地减少了人为操作误差,增大了测量结果验证的可重复性,测量效率高, 测量结果更加精确,测量准确度可达97%以上,测量读数在0.01mm位,其中三维点云模型的深度识别在0.001mm 位,明显优于其他测量方法,满足孔探工作中越来越高的测量精确要求。
三、多种测量模式下的比较分析
每一种测量方法都有很多测量模式,如长度、点到线、面积等等,这些模式在采用工业内窥镜进行民航发动机孔探工作当中都有着非常重要的应用。
对于长度(点到点)、折线长度(多线段)、面积的测量,单物镜阴影测量法、双物镜测量法和三维相位扫描测量法均可实现,但由于3D镜头的单视窗、广角设计,一次性有效测量区域是其他测量技术的两倍以上。对于发动机内较长的裂纹、划伤或者大面积的涂层脱落以及要确定损伤部位的相对位置等需要测量的缺陷或定位,采用三维相位扫描测量法有可能仅通过一次性操作即可获得精确的测量结果。而采用双物镜进行分段测量时,特征点不易被找到,或者边界点不好确定,有时为了分区还需要不断通过导向操作来改变镜头角度。需要几次测量操作之后再将结果累加,不仅工作量增加而且很难保证测量精度。较大面积的涂层脱落情况(如图10所示)使用三维相位扫描测量法均能够通过一次测量得到准确、有效的缺陷数据。
图7 对于点到线、深度(点到面) 的测量,单物镜阴影测量法和双物镜测量法虽然也可以实现,但前者需要探头上的测量镜头与被测物垂直而不便于操作,后者因为其成像及测量原理反馈到屏幕上的是二维平面信息,操作者也只能凭借经验在二维画面上人为操作放置测量点,无法进一步验证测量点在三维空间上选取的位置准确与否。尤其是对叶片缺口(见图11和图12)和叶尖与机匣间隙(见图13和图14)的测量,进行这种测量时,很容易把测量点放在被测叶片以外的区域,如另外的叶片上或机匣上,导致测量结果出现严重偏差(见图15)。而使用三维相位扫描测量法时,可生成三维点云图,通过旋转点云图像,从不同角度检查所选测量点的位置准确性,一旦发现测量点位置漂移, 可及时纠正。真正实现了测量后操作者仍可自行检查测量点定位是否正确,极大地降低测量时出现人为操作误差的概率。
此外,三维立体相位扫描测量技术还增加了深度剖面测量等新型的测量模式。仅需选择两个测量点,系统就会自动在两点之间画一条线,建立垂直于扫描表面的截面,可以直接得到剖面最深点(见图16),生成剖面视图(见图17),沿剖面的所有点的深度都可以直接测出,通过三维点云图(见图18)可以一次得到测量区域内最深点的位置和深度值,有助于对缺陷的形成原因、性质及缺陷发展趋势进行判断,有助于对叶片上的凹坑、掉块、烧蚀等损伤的深度测量。若使用双物镜测量法的深度模式,则需要先放置3个测量点,建立一个基准平面,然后在凹坑或掉块内手动选取“最深点”,通过深度值的实时显示人为地判断该区域最深点位置。因手动选点的数量有限,将导致测量结果的可重复性差,测量精度不能被保证,且测量效率低。
四、结束语
从孔探工作的工作效率、观察效果、测量精度以及设备安全等诸多因素考虑,三维相位扫描测量技术是非常适用于发动机孔探工作的一项先进技术。一套完善的孔探设备应当支持三维扫描测量功能,并兼备其他类型(如双物镜测量、阴影测量、比较测量等)的测量功能,以满足各种孔探环境下的测量需要。
自2010年年底美国韦林工业内窥镜推出三维相位扫描测量技术以来,该技术经过了发动机厂家以及国内外众多航空公司的应用验证,其技术成熟度和实用性都较高,现已成为了民航发动机孔探领域的主要测量技术。国航工程技术分公司成都维修基地于2013年引进该项测量技术,大大提高了孔探工作的效率和精确度。
相关推荐:相位扫描三维立体测量工业内窥镜 MViQ