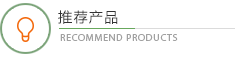
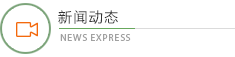

韦林工业内窥镜测量功能新亮点:自动识别并测量缺陷最深点或最高点
作为可视化检测工具,工业内窥镜不仅具有定性观察的能力,而且还可以测量缺陷(以及特定目标对象)的量化指标。像裂纹深度、凹坑深度、磨损槽深度、焊缝高度等这一类测量,往往涉及缺陷的最深点或最高点。韦林工业内窥镜测量功能新亮点:利用单物镜相位扫面三维立体测量功能(3DPM)的深度剖面测量或区域深度剖面测量技术,可自动识别缺陷最深点或最高点,并显示相应深度数值。为了便于描述,下面重点以最深点为例进行介绍,最高点同理。
在韦林工业内窥镜推出上述亮点功能之前,传统的深度测量过程采用点到面的测量方法:先由检测人员在测量图像呈现的轮廓表面选择三个点,系统据此确定一个平面,然后再测量选定的第4个点——最深点到该平面的距离。在该过程中,可能由于选点偏差导致使用的并非理想平面,而且最深点的选择往往也需要检测人员多次移动操纵杆进行尝试,因此传统测量方法存在结果不准确以及测量效率低的问题。
韦林工业内窥镜推出的深度剖面测量技术,使得上述问题迎刃而解。采用深度剖面测量技术,系统会自动根据检测人员选定的两个点确定一个剖面、并自动识别剖面上的最深点。也就说检测人员只需要在轮廓表面选择两个点,系统就会自动测量出垂直剖面内的最深点的深度值。
深度剖面测量的优势体现在:
1. 系统自动识别最深点,不用检测人员反复试探查找;
2. 系统直接给出最深点的准确深度值,不存在因为人为选点确定平面引入的偏差;
3. 具有剖面视图,方便检测人员查看剖面上的缺陷走向,并可以通过操纵杆在缺陷走向上随意移动光标位置,而系统则会实时显示光标位置处的深度值,方便检测人员同步了解剖面内其他缺陷位置的深度信息;
4. 在剖面视图上还可以显示为确定剖面所选的两点间距离,辅助检测人员评估最深点的分布位置。
再介绍一下区域深度剖面测量,即:系统在检测人员设定的三个光标所定义的区域内,自动扫描一系列剖面、确定具有最低点的剖面,并自动给出最低点的深度值。该技术自动在指定区域内的一系列剖面内测算最深点,除具有与深度剖面测量同样的优势外,还能够准确测量弧型表面上的最深点,在涡轮叶片缺陷检测中具有很强的实用性。
综上,深度剖面测量和区域深度剖面测量技术,为内窥检测中的裂纹深度、凹坑深度、磨损槽深度、焊缝高度等测量应用提供了更为精准、快捷的测量手段。
韦林是美国进口工业内窥镜品牌,其出色的测量技术一直是业内模仿学习的标杆。韦林工业视频内窥镜 Everest Mentor Visual iQ 搭载的3DPM功能,除了具有本文介绍的两种测量方法外,还有空间平面缺失测量、叶片与机匣间隙自动测量、大尺寸叶片3D拼接缝合测量等创新测量方法。更多详情请关注本站文章或咨询北京韦林意威特工业内窥镜有限公司。
相关推荐:
【干货】什么是单物镜相位扫描三维立体测量技术?优势及案例分享
使用相位扫描3D测量内窥镜进行缺陷测量,无需更换镜头效率更高!
韦林工业内窥镜在发动机叶尖掉角检测及测量上的应用
工业内窥镜产品的核心技术有哪些?选购时应格外关注!
热点文章:
通过具体选型案例讲解工业内窥镜一般分为哪三种
工业内窥镜在新能源精细化工行业的检测应用
使用工业内窥镜检查航空发动机的正确操作方法
韦林工业内窥镜亮相电力行业金属专业技术监督工作会议